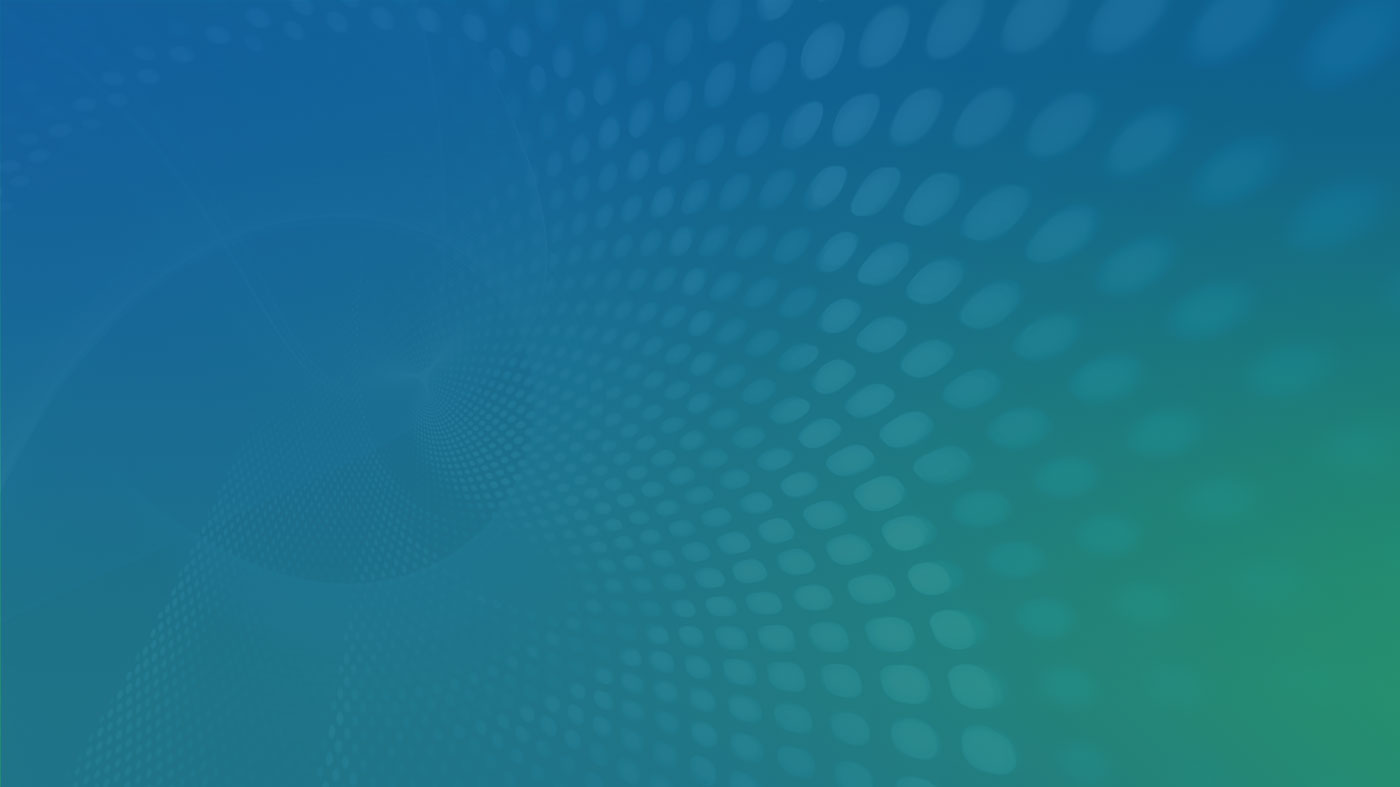
A8 series module
A GAME CHANGER IN THE SIDE-STREAM MBR APPLICATION
A8 Series Module
The Large Diameter A8 Modules permits simple, rapid, high area and inexpensive UF tubular filtration for new and existing installations in the waste water industry.
Processors today are faced with mounting pressure to reduce wastewater volumes and treatment costs. While environmental regulations and “green” politics create a demand for companies to cut effluent volumes, economics also plays a major role. Discharge costs for wastewater are rising, as are charges for disposal and landfill of sludge generated from traditional wastewater treatment systems.
Suitable for fluids with high viscosity &/or suspended solids as their wide flow paths make them highly resistant to blocking. Pre-treatment requirements are minimal – benefit that renders them the most cost-effective choice for many small systems
Key Applications
- Side stream MBR
- Recovery and reuse of water from waste streams
- Leachate
- Industrial Clarification
- Brine Recovery
- Food industry effluents
- Chemical Wastewater
- Textile Wastewater
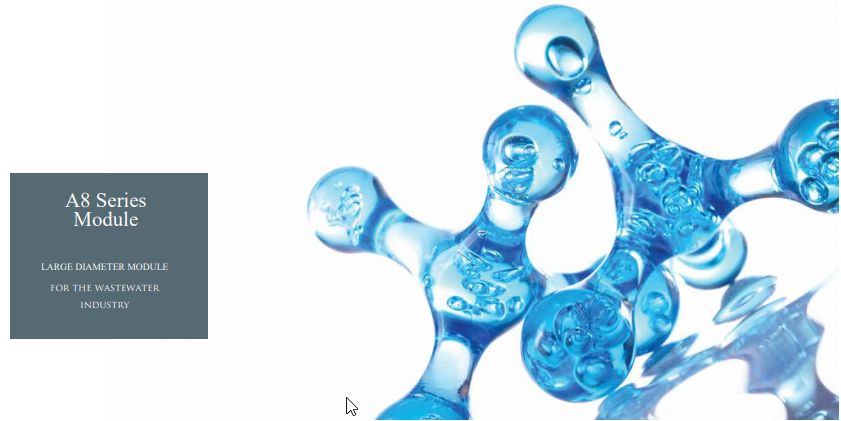
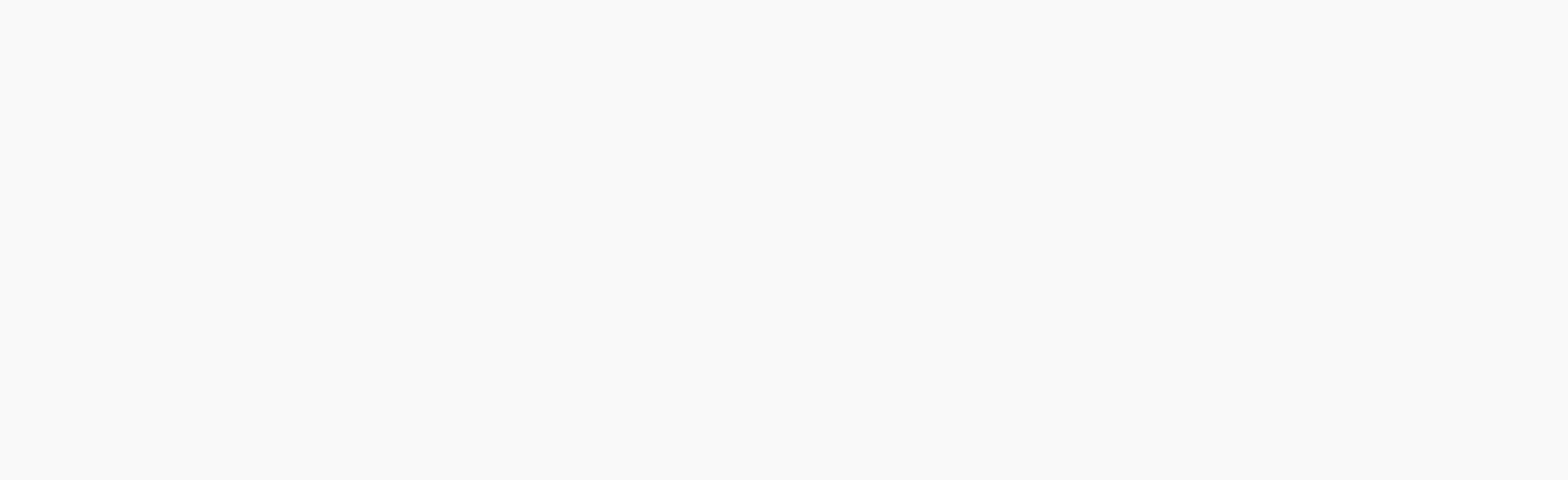
A8 Series Module Product Information
Introduction to A8 Series module
The A8 Series design permits a simple, rapid and inexpensive membrane replacement. Other advantages include a robust and low-cost module in GRP material. The module comprises of two main parts, the membrane core and the module shroud. The core is fixed into the shroud, end seals prevent leakage of feed and concentrate from the module. While the inner O-rings prevent leakage of permeate. Modules are usually connected in series with U-bends.
The membrane core
The membrane core consists of several membrane tubes potted together at each end to form a rigid tube bundle. Figure 2 shows the cross-section of a membrane tube. The inside layer of the tube is the thin semi permeable polymeric membrane. It is the membrane layer which separates the feed liquid into two streams. A range of membrane types is available, each offering different separation characteristics.
The middle and outer layers are the support tube for the membrane.

The module shroud
This is the housing or vessel for the membrane core. Permeate passing through the membrane collects in the shroud before flowing out to permeate storage.
The standard shroud material is made of a glass reinforced plastic (GRP). shrouds are available 3 and 4 meter lengths.
The membrane core is fixed into the shroud. All shrouds have two off-takes – one at each end for permeate to exit the module. The shrouds must be positioned with their offtakes vertically aligned (one at the top, the other at the bottom). During all process and cleaning operations, permeate flows out of both shroud off-takes. The top off-take allows air to enter and exit during shroud filling and draining operations.
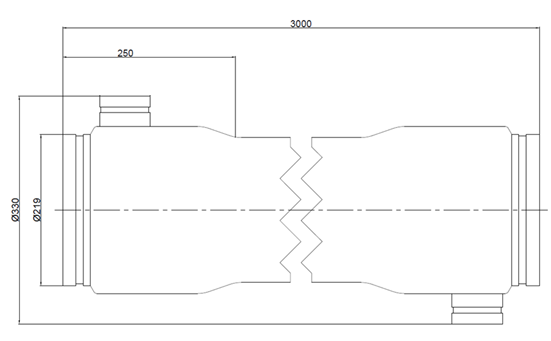
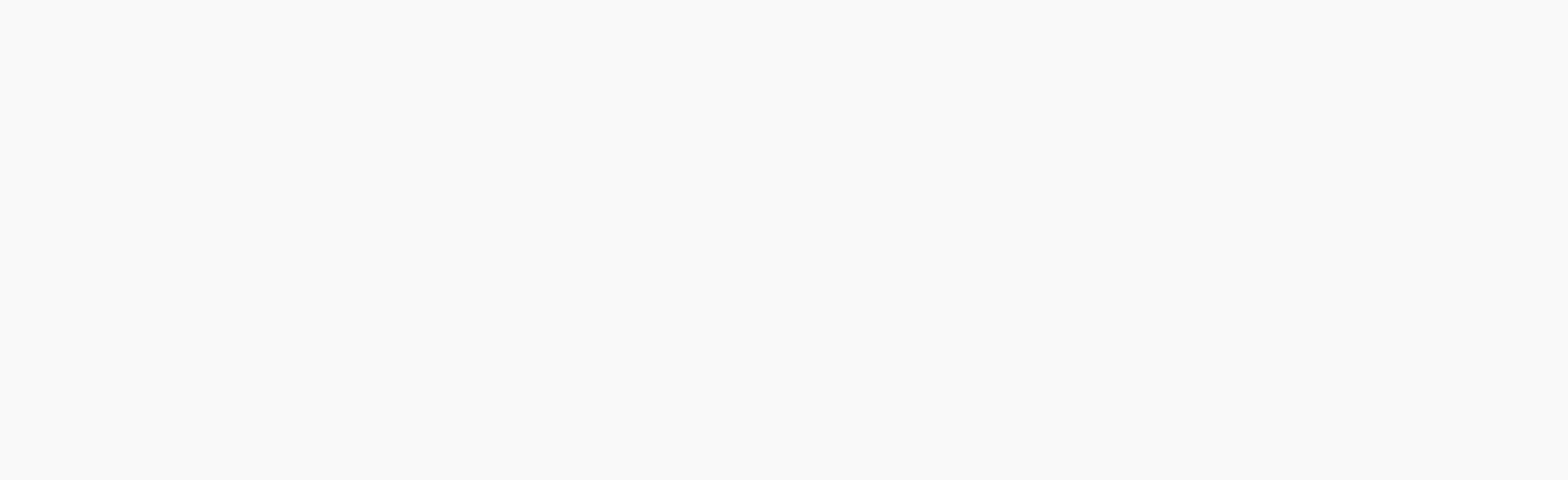
Operating limits for A8 Series modules
To ensure maximum life from the modules the following operating limits must not be exceeded:
Membrane Operation Limits | |
---|---|
Max Operating Pressure | 8 bar |
Max Operating Temperature | 49◦C |
pH Range | 1.5 – 10.5 |
Max Chlorine Exposure | 250 ppm at pH >9 |
Shroud-side Pressure | Never exceed tube-side pressure |
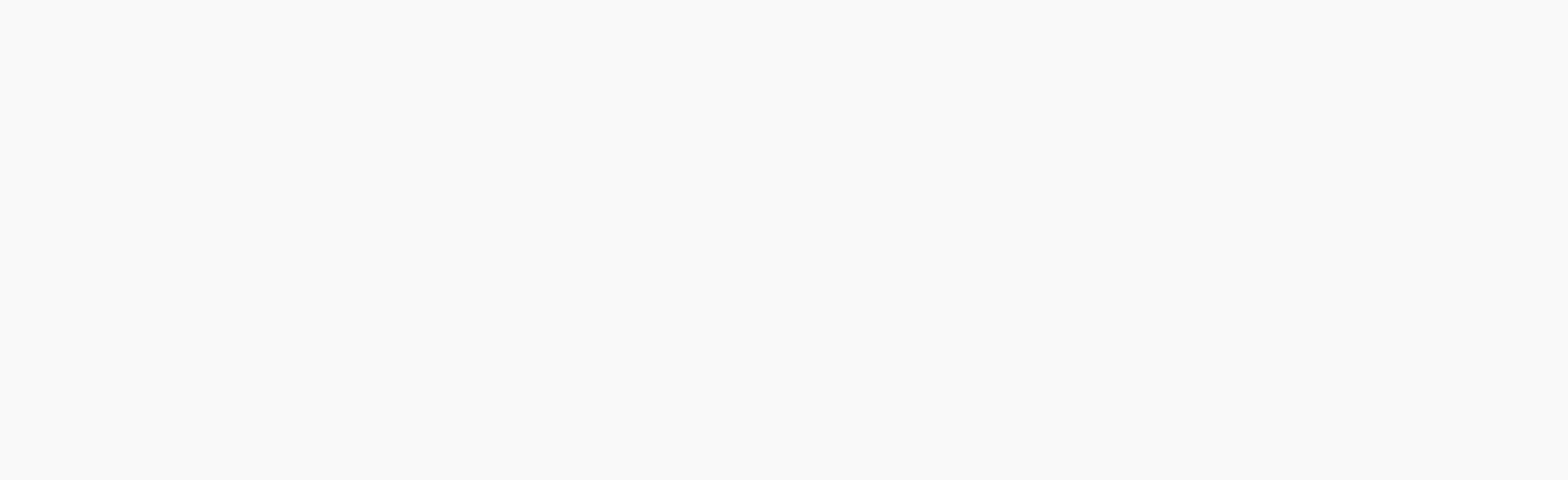
PCI Membranes’ Side-Stream Membrane Configuration Advantages
✓ Perfect replacement to competitor products with 27m2 and 36m2 membrane area.
✓ Unique offer to install tubular UF membranes with cut off 20k Da, 100k Da, 200k Da, 450k Da separation point in an 8 inch housing.
✓ Less frequent and simpler membrane cleaning operation.
✓ Simpler membrane maintenance: the maintenance of the submersed membranes is far more complex than that required to maintain the efficiency of a side-stream membrane: submersed membranes need to be removed from the basin with all its operational logistic, environmental consideration and messy problems.
✓ Optimum engineering, personal health and safety design: ability of intervening on the ultrafiltration membrane modules without any direct contact with the activated sludge or wastewater fluids.
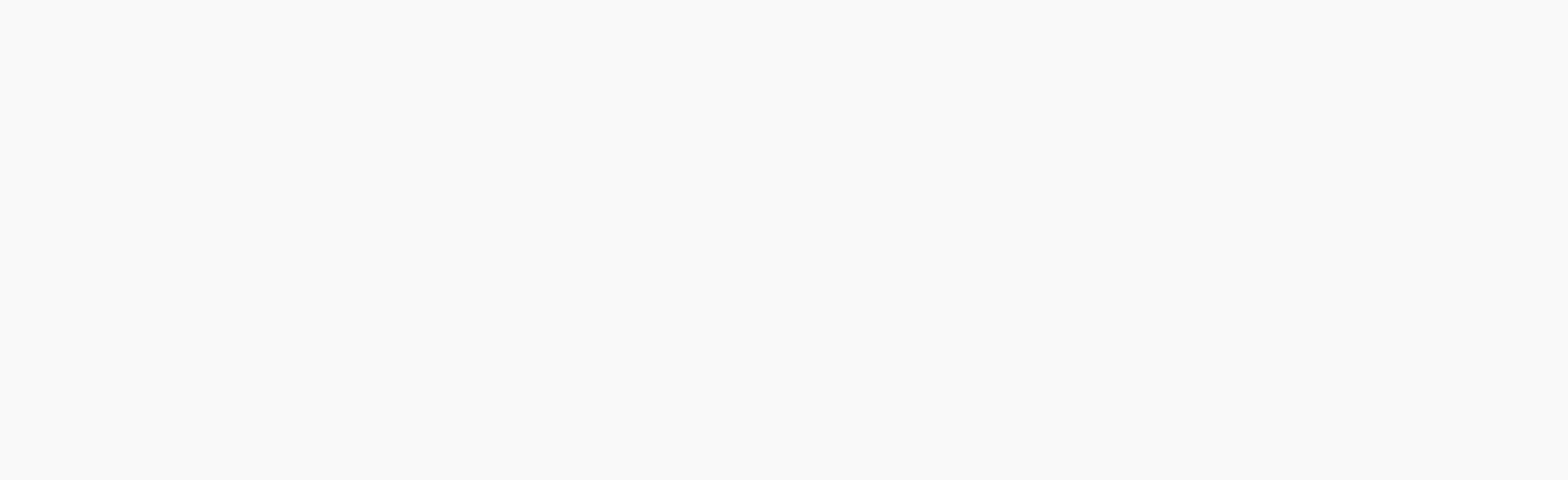
Data Sheets
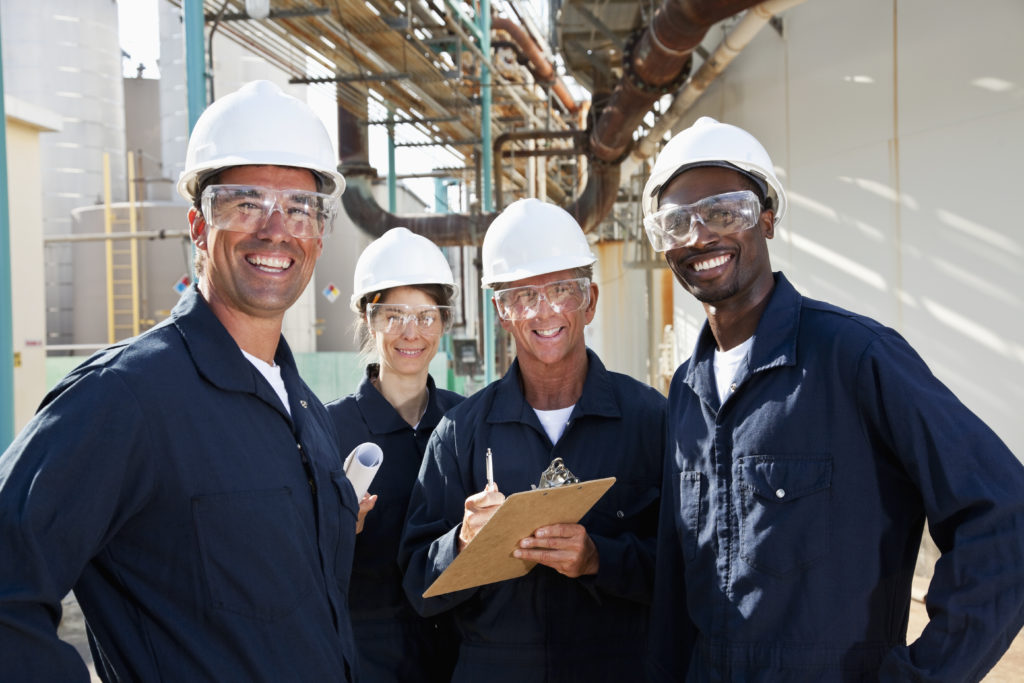
Request Information
We offer process solutions for a wide variety of filtration applications using microfiltration, ultrafiltration, nanofiltration and reverse osmosis technologies.