Multi-stage Treatment of Landfill Leachate: Case Study in Germany
BACKGROUND
At Damsdorf in Germany, the existing 15 hectare landfill site, which had no bottom sealing or leachate collection system was approaching capacity. A new site was constructed in 2 sections, each of 6 hectares, with a total refuse capacity of 3 million cubic metres. This new site had bottom and topsealing systems, and a leachate treatment system incorporating biological pretreatment using ultrafiltration and reverse osmosis for leachate concentration.
FILLING & LEACHATE COLLECTION
In order to minimise the time taken to achieve methanogenesis when the site was new, a special filling leachate collection method was used. Each of the main sections of the landfill were subdivided into a number of compartments. The first compartment was layered with compacted and loose refuse comprising materials from the old site mixed with new. This reduced the time taken to achieve methanogenesis from the normal 2 years to about 9 months. When compartment 1 was full, the other compartments were used. Leachate from all compartments is taken through compartment 1 (which is in the methanogenic phase) before collection. This ensured that the quality of the leachate changed only gradually after the first year of operation.
BIOLOGICAL PRETREATMENT / ULTRAFILTRATION
Biological pretreatment uses the Activated Sludge Process, which comprises prefiltration, denitrification in a 125m3 stirred tank, and two 125m3 aeration tanks. The tubular ultrafiltration (UF) system recovers the biomass post-nitrification. A 10-fold concentration of biomass is achieved, and the concentrated biomass is recycled to the de-nitrification stage. Approximately 3% of the UF permeate (biologically-pretreated leachate) is recycled to the aeration tanks for foam control.
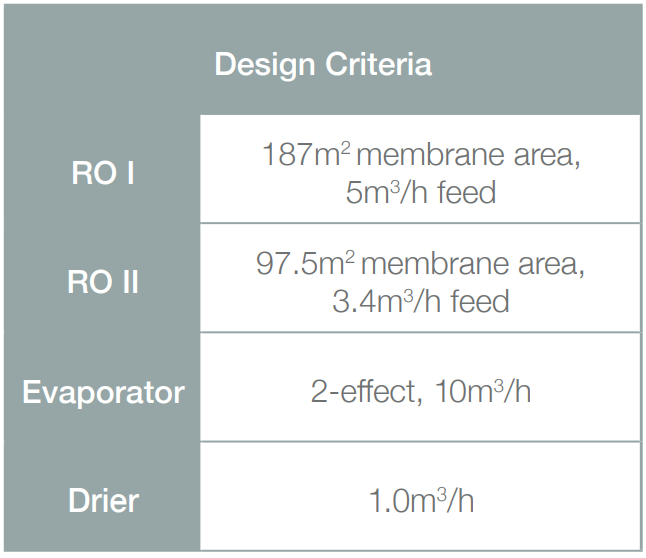
REVERSE OSMOSIS
The UF permeate is concentrated by 2-stage RO. The first stage uses PCI’s tubular membrane system, and achieves a concentration factor of up to 5. The permeate from the first stage is then concentrated in the second stage, which uses PCI’s spirallywound membrane system and achieves a concentration factor of 4. Both stages operate at 40-50 bar as well as ambient temperature, and are chemically cleaned on a weekly basis. The cleaning solution is returned to the biological pretreatment process. The concentrate from the second stage is returned to the first stage.
CROSSFLOW MEMBRANE TECHNOLOGY
- Reduces pollutants and contaminants
- Meets local water discharge legislation
- Increases efficiency & effectiveness of biological treatment systems
- Provides a cost-effective means of treating leachate with minimum space requirements
- Treats a variety of leachate types
- Designed to meet specific site demands, e.g. fluctuations in volumes and composition
EVAPORATION
The installation comprises a 2-effect evaporator which achieves a 10-fold concentration.
RAW LEACHATE QUALITY
- Leachate volume – average (m3/d) 80
- COD (mg/l) 5,000
- BOD (mg/l) 500
- Ammonia (mg/1) 1,500
- AOX (mg/l) 3.5
- Conductivity (mS/cm) 18